ISO 50001 | Energy Management
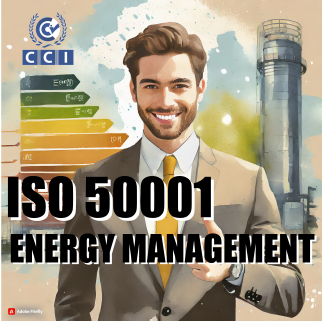
Energy Management systems | EMS
Requirements with guidance for use, is a voluntary International Standard developed by ISO (International Organization for Standardization). ISO 50001 gives organizations the requirements for energy management systems (EnMS). ISO 50001 benefits organizations large and small, in both public and private sectors, in manufacturing and services, in all regions of the world. ISO 50001 will establish a framework for industrial plants, commercial, institutional, and governmental facilities, and entire organizations to manage energy. Targeting broad applicability across national economic sectors, it is estimated that the standard could influence up to 60 % of the world's energy use. ISO 50001 energy management standards identify requirements for an organization to establish, implement, sustain, and improve an Energy Management System (EnMS), this enables the organization to take a deliberate approach to continually improve energy performance. This new standard will establish an international structure to help manage the energy supply, uses, and intake of industrial, commercial, or institutional organizations, which includes measurement, documentation, reporting, design, and procurement practices for energy-using equipment, systems, and processes. ISO 50001 energy management standard applies to all aspects impacting energy use, and this can be monitored and influenced by an organization.
Implementing ISO 50001 Helps Your Company In The Following Way:
- Enables the organization to establish the system and processes required to improve energy commandment, which includes energy efficiency use consumption, and intensity
- Reductions in energy cost. GHG emissions and other environmental impacts, through the systematic management of energy
- Demonstrate that the organization implemented sustainable energy management systems, completed a baseline of energy use, and focused on continuously improving their energy vividness